Fine Beautiful Info About Is SCADA A PLC Or DCS

Unraveling the Mysteries
1. The Alphabet Soup of Industrial Automation
Okay, let's be honest. The world of industrial automation can feel like navigating a bowl of alphabet soup. SCADA, PLC, DCS—it's enough to make your head spin! But don't worry, we're here to break it down in a way that's actually (dare I say it?) understandable. Think of me as your friendly neighborhood automation translator.
The core question we're tackling today: Is SCADA a PLC? Is it a DCS? Or is it, perhaps, something completely different? To answer that, we need to understand what each of these technologies actually does.
Imagine you're running a massive water treatment plant. You have pumps, valves, sensors, and all sorts of other equipment working in concert. These components require to works as per required, automatically. All this is to ensure clean, safe drinking water for the community. Someone needs to monitor and control it. That's where these systems come into play. They provide the backbone for efficient, automated operations.
In the simplest terms, think of it like this: They are the orchestra that makes your water plant sing, making sure all the instruments (the pumps, valves, etc.) are playing the right notes at the right time.
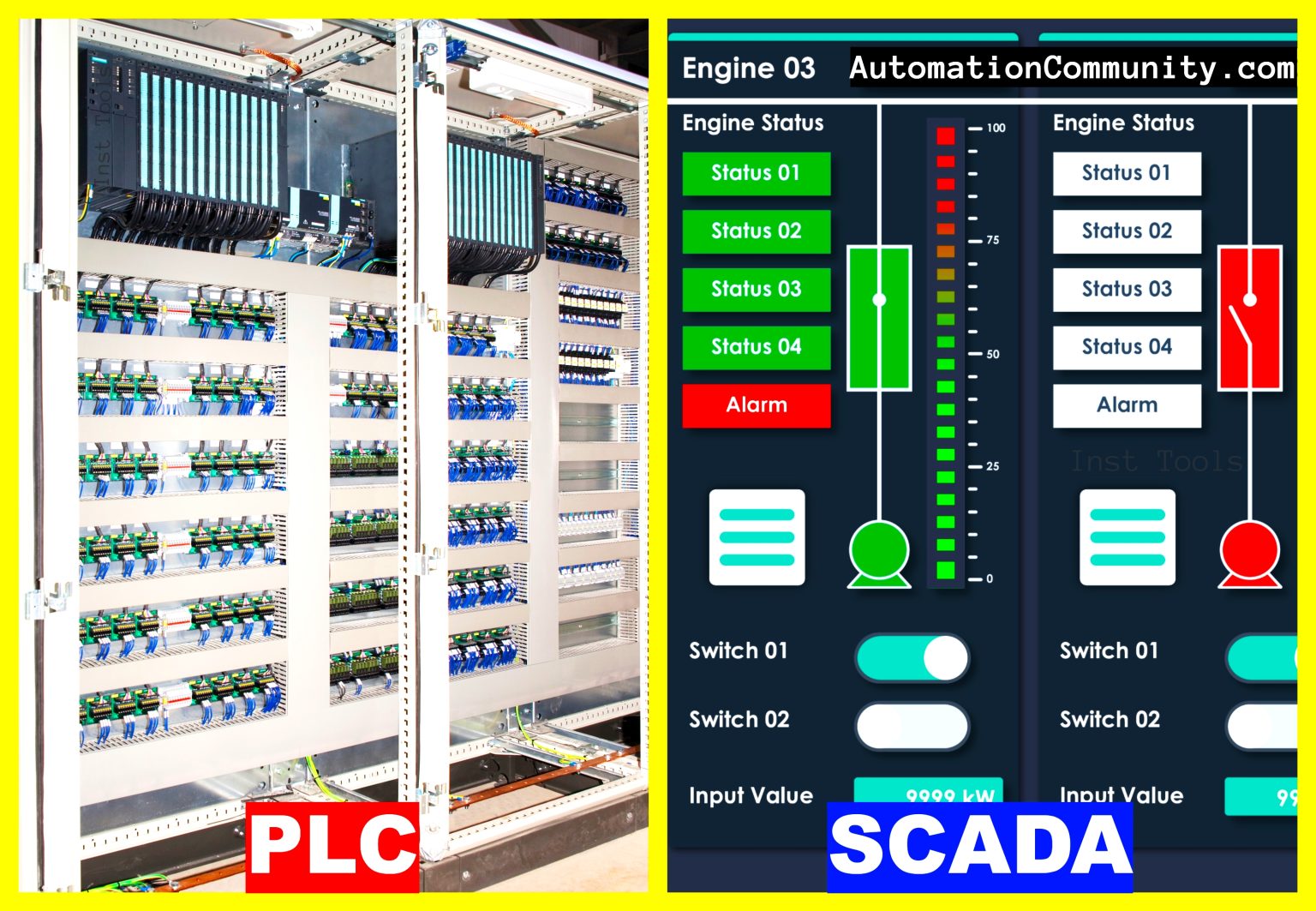
Difference Between PLC And SCADA Automation Community
PLC
2. Getting Down to the Programmable Logic Controller Basics
Let's start with PLCs, or Programmable Logic Controllers. These little guys are the workhorses of the automation world. Think of them as dedicated, single-task robots. They're built to control specific processes or machines, and they do it with impressive reliability.
A PLC is essentially a specialized computer designed to control a specific task. It takes in information from sensors (temperature, pressure, flow rate, etc.), processes that information according to a pre-programmed logic, and then sends out signals to control actuators (valves, motors, pumps, etc.). Imagine a coffee maker; the PLC would monitor water levels, heating element temperature, and control the flow of water to brew your morning cup.
PLCs excel at fast, real-time control. They are designed to respond quickly and predictably to changes in their environment. You'll find them controlling everything from assembly lines and robotic arms to traffic lights and amusement park rides. If a process requires precise, immediate control, chances are a PLC is involved.
Key characteristics of a PLC include its rugged design (built to withstand harsh industrial environments), its deterministic behavior (meaning it will always react the same way to the same input), and its ease of programming (using languages like ladder logic, function block diagrams, and structured text).
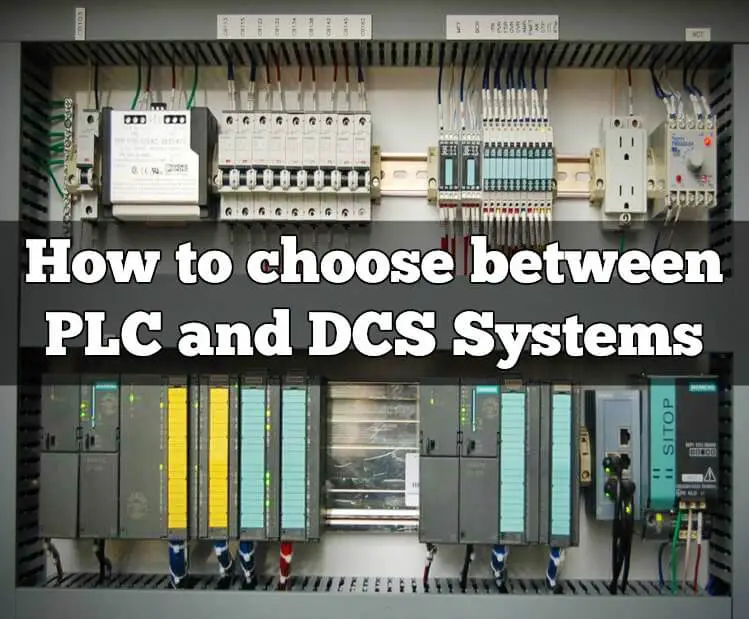
DCS
3. Delving into Distributed Control Systems
Now, let's move on to DCS, or Distributed Control Systems. If PLCs are the individual musicians, a DCS is the conductor of the entire orchestra. DCSs are designed to manage complex, geographically dispersed processes, such as those found in oil refineries, chemical plants, and power generation facilities. They involve multiple controllers managing parts of the whole operation.
Instead of a single controller handling everything, a DCS uses a network of interconnected controllers, each responsible for a specific section of the process. This distributed architecture offers several advantages, including increased reliability (if one controller fails, the rest of the system can continue to operate), scalability (it's easy to add or remove controllers as needed), and improved performance (by distributing the processing load).
Think of a large oil refinery. A DCS would manage everything from the flow of crude oil through the various processing units to the temperature and pressure of the reactors to the blending of finished products. It would also provide operators with a centralized view of the entire operation, allowing them to monitor performance, identify potential problems, and make adjustments as needed.
DCS systems typically include advanced features such as process optimization, alarm management, historical data logging, and advanced control algorithms. They are designed to provide a comprehensive, integrated solution for managing large-scale, complex industrial processes.
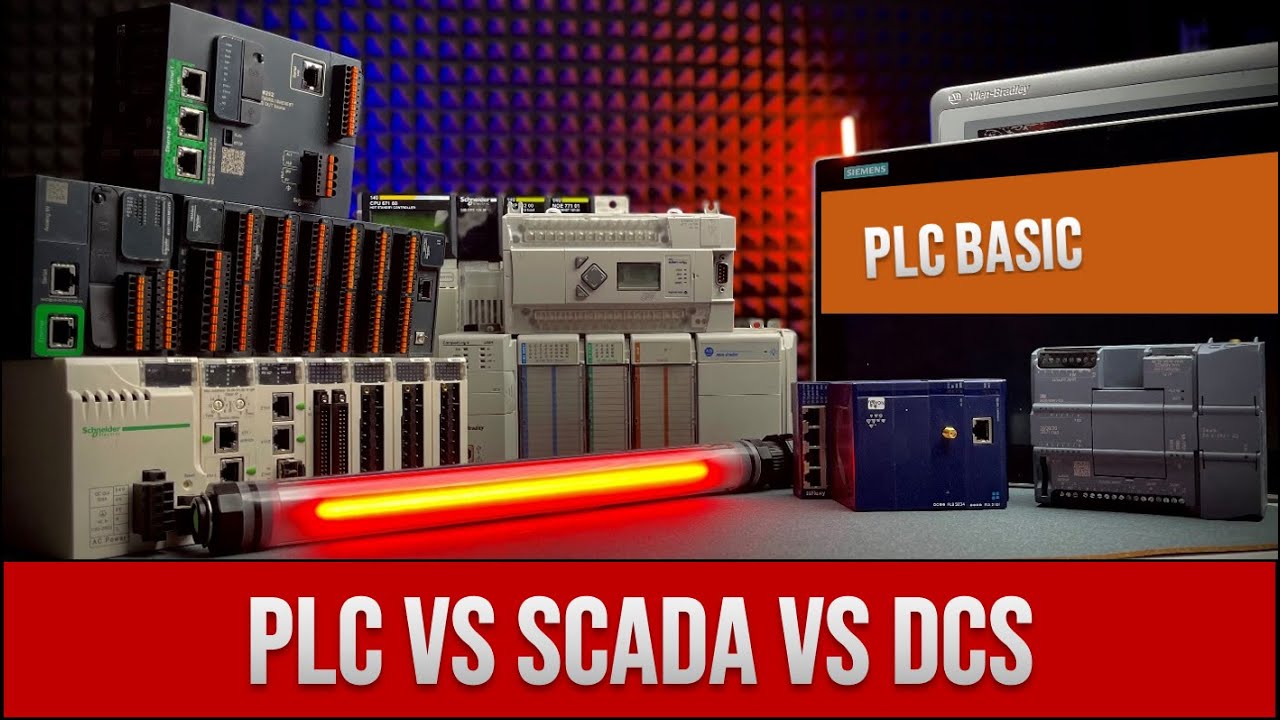
SCADA
4. Supervisory Control and Data Acquisition Explained
And now for the star of our show: SCADA, or Supervisory Control and Data Acquisition. SCADA systems are designed to monitor and control processes over large geographical areas. Think of pipelines, power grids, water distribution networks, and other infrastructure systems that span vast distances.
Unlike PLCs and DCSs, which focus on controlling individual processes or plants, SCADA systems provide a supervisory layer of control. They collect data from remote sites (using PLCs or other controllers), transmit that data to a central location, and allow operators to monitor and control the entire system from a single interface.
Imagine a city's water distribution network. A SCADA system would monitor water levels in reservoirs, flow rates in pipelines, and pressure at various points throughout the system. It would also allow operators to remotely control pumps, valves, and other equipment to maintain optimal water pressure and flow.
SCADA systems typically include features such as remote terminal units (RTUs) to collect data from remote sites, communication networks to transmit data, human-machine interfaces (HMIs) to display data and allow operator interaction, and historical data storage for analysis and reporting. They are designed to provide a comprehensive, real-time view of the entire system, enabling operators to make informed decisions and respond quickly to changing conditions.
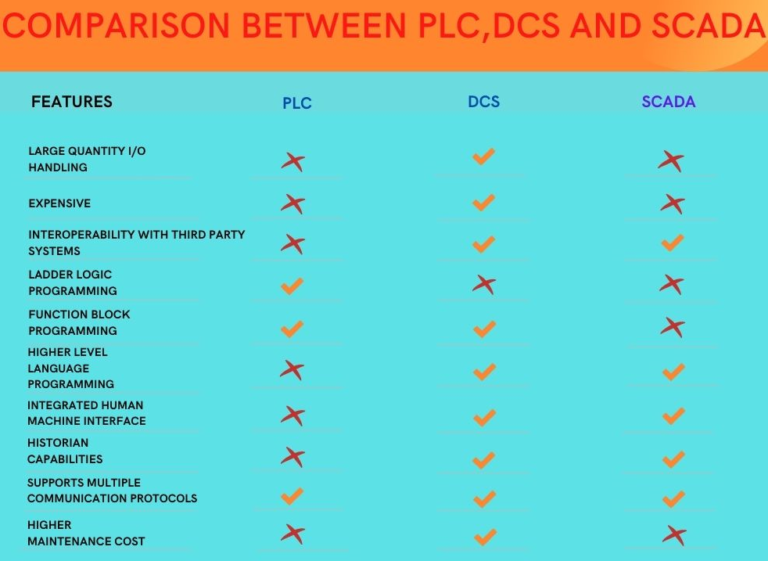
Comparison Between PLC, DCS, And SCADA Instrumentation Control
So, Is SCADA a PLC or a DCS? The Answer, Finally!
5. Putting It All Together
Okay, drumroll please... The answer is: Neither! SCADA is not a PLC, and it's not a DCS. It's a different type of system altogether.
Think of it this way: PLCs are the individual components controlling specific tasks. DCSs manage complex processes within a single plant. And SCADA sits above both of them, providing a supervisory layer of control over geographically dispersed assets. SCADA uses both PLCs and DCSs to gather the data. They are the eyes, ears, and hands at the remote site.
A SCADA system might use PLCs to control individual pumps and valves at a remote pumping station. It might use a DCS to manage the operations of a water treatment plant. But the SCADA system itself is responsible for collecting data from all of these sources, transmitting it to a central location, and allowing operators to monitor and control the entire network.
In essence, SCADA, PLC, and DCS are all pieces of the same puzzle, each playing a distinct role in the automation landscape. Understanding their differences and how they work together is crucial for designing and implementing effective industrial automation solutions.

What Are The Roles Of DCS And SCADA In Digital Transformation
Wrapping Up
6. A Final Word on Industrial Automation
So, there you have it! Hopefully, you now have a clearer understanding of the differences between SCADA, PLCs, and DCSs. Remember, PLCs control individual tasks, DCSs manage complex processes within a single plant, and SCADA provides a supervisory layer of control over geographically dispersed assets.
Choosing the right system for a particular application depends on a variety of factors, including the complexity of the process, the geographic scope, the required level of control, and the budget. Often, a combination of all three technologies is used to create a comprehensive automation solution.
It's also important to remember that these technologies are constantly evolving. New features and capabilities are being added all the time. Keeping up with the latest trends is essential for staying ahead of the curve and maximizing the benefits of industrial automation.
The world of industrial automation is a complex one, but with a little understanding, it can be navigated successfully. So, go forth and automate! And don't be afraid to ask for help along the way. There are plenty of resources available to assist you in your journey.