Great Tips About How Do Digital Torque Sensors Work
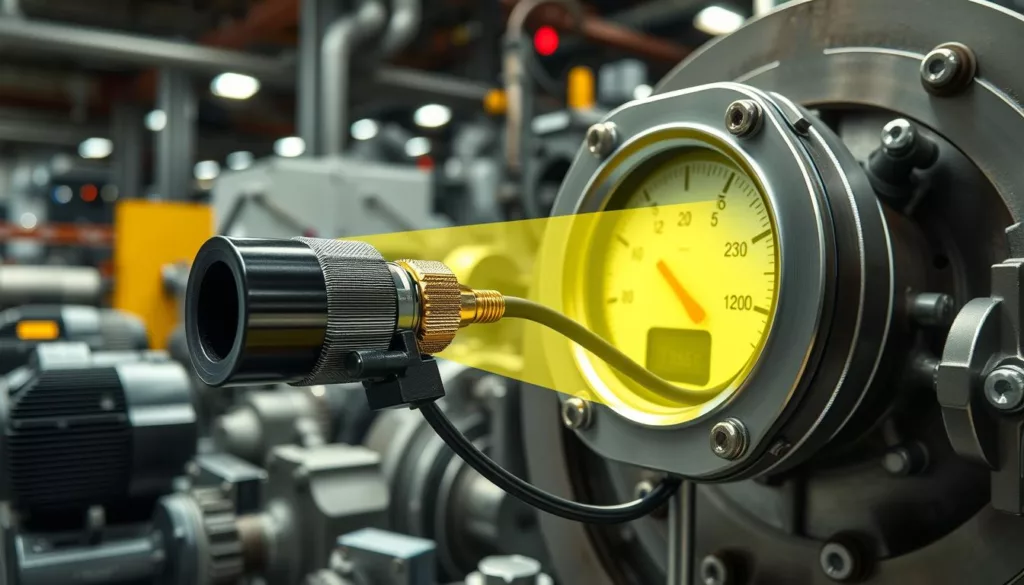
Understanding Torque Sensors In Industrial Applications
Unlocking the Secrets of Digital Torque Sensors
Ever wondered how those high-tech tools in workshops and labs precisely measure the twisting force on a bolt or a rotating shaft? The answer lies within digital torque sensors, those unsung heroes of precision measurement. They're not just about tightening screws; they're critical in ensuring the safety and reliability of everything from your car's engine to the wings of an airplane. Let's dive into the fascinating world of these gadgets and see what makes them tick. Think of it as peeking behind the curtain to understand the magic.
At its core, a digital torque sensor is a sophisticated device designed to accurately measure torque, which is essentially a twisting force that tends to cause rotation. What sets these sensors apart from their analog counterparts is their ability to convert the mechanical torque into a digital signal. This digital output can then be easily processed, displayed, and recorded by computers or other digital systems, providing a highly precise and reliable measurement. Understanding this conversion process is key to appreciating how these sensors function.
1. What is Torque and How Does it Relate to Sensors?
Torque, in simple terms, is the measure of the force that can cause an object to rotate about an axis. Imagine using a wrench to tighten a bolt: the force you apply to the wrench handle creates torque, which then tightens the bolt. The amount of torque depends on both the force you apply and the distance from the axis of rotation (the bolt) to the point where you apply the force. The longer the wrench, the more torque you can apply with the same amount of force! Clever, eh?
Now, how does this relate to sensors? Well, torque sensors are designed to quantify this twisting force. They act as the 'measuring cups' for rotational force, giving engineers and technicians precise readings. This precision is crucial in countless applications, from manufacturing processes to quality control, and even in research and development. Without accurate torque measurement, things could literally fall apart!
The real trick, and where the magic happens, is in how these sensors translate physical twisting into something a computer can understand. Thats where the digital aspect comes in. It's about converting mechanical strain into an electrical signal, then cleaning it up and presenting it as a nice, neat number. But we're getting ahead of ourselves. Let's look at the main components of a digital torque sensor.
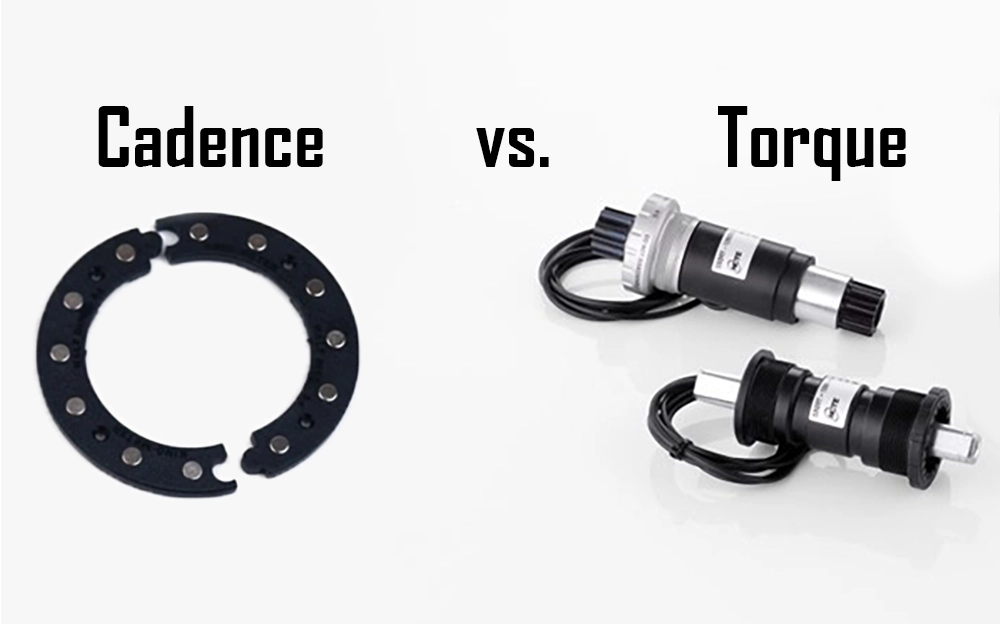
Torque Vs. Cadence EBike Sensors All Differences Explained
The Anatomy of a Digital Torque Sensor
Like any good gadget, a digital torque sensor is made up of several crucial parts working in harmony. Here's a breakdown of the key players:
2. Strain Gauges
Strain gauges are the workhorses of a torque sensor. These tiny resistors are bonded to the sensor's shaft or body. When torque is applied, the shaft twists slightly, causing the strain gauges to either stretch or compress. This change in shape alters their electrical resistance. It's a tiny change, but a crucial one.
Imagine a rubber band. When you stretch it, it becomes thinner and its resistance to being stretched further increases (think of it as 'resisting' more). Similarly, strain gauges change their resistance proportionally to the amount of strain they experience. This change in resistance is then measured to determine the applied torque.
Different types of strain gauges exist, but the most common ones used in torque sensors are foil strain gauges. These are incredibly thin and flexible, allowing them to conform precisely to the shape of the sensor's body. They are also very sensitive, which is essential for accurate torque measurement. The sensitivity of the strain gauges contributes directly to the overall precision of the sensor. The more sensitive the gauge, the smaller the change in torque it can detect. This is vital for applications that require incredibly precise torque measurements, such as in medical devices or aerospace engineering.
3. Wheatstone Bridge
The small change in resistance from the strain gauges isn't enough to be directly useful. That's where the Wheatstone bridge comes in. This clever circuit is used to amplify the tiny changes in resistance from the strain gauges into a more measurable voltage signal.
A Wheatstone bridge consists of four resistors arranged in a diamond shape. The strain gauges are incorporated into this bridge, so when torque is applied and the strain gauges change resistance, the bridge becomes unbalanced. This imbalance produces a voltage difference that is proportional to the applied torque. The bigger the imbalance, the greater the torque.
The Wheatstone bridge is a really cool piece of engineering because it allows you to accurately measure even the smallest changes in resistance. It's like having a super-sensitive amplifier that can detect the faintest whispers of torque. This amplification is absolutely essential for achieving the accuracy that digital torque sensors are known for.
The configuration of the Wheatstone bridge is also very important for temperature compensation. Because the resistance of the strain gauges can also be affected by temperature, special care must be taken to ensure that the voltage output of the bridge is only proportional to the applied torque. This is typically achieved by using matched strain gauges and resistors that have similar temperature coefficients. This ensures that changes in temperature will affect all components of the bridge equally, thereby cancelling out any temperature-induced errors.
4. Analog-to-Digital Converter (ADC)
The amplified voltage signal from the Wheatstone bridge is still analog, meaning it's a continuous signal. Computers, however, speak in digital, which is a series of discrete values (think of it as on/off switches). The ADC bridges this gap.
The ADC converts the analog voltage signal into a digital representation that can be understood by a computer or microcontroller. It samples the analog signal at regular intervals and assigns a digital value to each sample. The higher the resolution of the ADC (the number of bits it uses), the more accurate the digital representation will be.
Think of it like translating a foreign language. The analog signal is like a sentence spoken in an unknown tongue, and the ADC is the translator that converts it into a language the computer understands. The better the translator (higher resolution ADC), the more accurate the translation, and the more precise the torque measurement. A good ADC is vital for a high-quality digital torque sensor, influencing both accuracy and speed of the sensor.
5. Digital Signal Processing (DSP)
Even after the ADC does its job, the digital signal might still contain some noise or unwanted variations. This is where digital signal processing (DSP) comes in to refine the output.
DSP algorithms are applied to the digital signal to filter out noise, compensate for any non-linearities in the sensor's response, and improve the overall accuracy and stability of the measurement. This can include techniques like averaging multiple readings, applying digital filters, and implementing calibration curves to correct for any systematic errors.
Imagine you're trying to listen to someone speaking in a crowded room. DSP is like a super-powered hearing aid that filters out the background noise, allowing you to hear the speaker clearly. It ensures that the final torque reading is as clean and accurate as possible.
DSP is especially important in applications where high accuracy and repeatability are critical, such as in aerospace, automotive, and medical industries. It allows digital torque sensors to deliver reliable and consistent performance, even under challenging operating conditions. With sophisticated DSP, the sensor can compensate for factors like temperature drift and signal interference, ensuring the integrity of the torque measurement.

Rotary Torque Sensor Transducer Measurement Meter Datum Electronics
How it all Works Together
So, how does all this magic come together to measure torque? Let's break it down step-by-step:
6. Step 1
First, torque is applied to the sensor's shaft or body. This could be from tightening a bolt, twisting a shaft, or any other rotational force.
7. Step 2
The applied torque causes the sensor's shaft to twist slightly, which in turn strains the strain gauges bonded to it. This strain changes the electrical resistance of the strain gauges.
8. Step 3
The change in resistance of the strain gauges unbalances the Wheatstone bridge, producing a voltage signal that is proportional to the applied torque.
9. Step 4
The analog voltage signal from the Wheatstone bridge is converted into a digital signal by the ADC.
10. Step 5
DSP algorithms are applied to the digital signal to filter out noise, compensate for errors, and improve the overall accuracy of the measurement.
11. Step 6
Finally, the processed digital signal is displayed on a screen or transmitted to a computer or other device for further analysis or control. You get a nice, clean number representing the amount of torque applied.

Applications of Digital Torque Sensors
Digital torque sensors are incredibly versatile and find applications in a wide range of industries. Here are just a few examples:
12. Manufacturing
In manufacturing, torque sensors are used to ensure that bolts and fasteners are tightened to the correct torque specifications. This is crucial for ensuring the reliability and safety of products, from cars to appliances to airplanes. Too little torque and the fastener might come loose; too much and it could break. Digital torque sensors help manufacturers find that "Goldilocks zone" of just the right tightness.
The use of digital torque sensors in manufacturing has become increasingly prevalent due to the stringent quality standards and regulations. Torque sensors enable real-time monitoring and control of the tightening process, allowing manufacturers to identify and correct any deviations from the specified torque values. This not only improves product quality but also reduces the risk of product recalls and warranty claims.
Furthermore, digital torque sensors are often integrated with automated assembly systems, providing feedback to the control system and ensuring that each fastener is tightened correctly. This automation not only improves efficiency but also reduces the potential for human error. Advanced torque sensors can even store torque data for traceability purposes, providing a complete record of the tightening process for each product.
The ability to precisely control and measure torque during assembly is vital for maintaining the integrity and longevity of manufactured products. By utilizing digital torque sensors, manufacturers can ensure that their products meet the highest quality standards and provide reliable performance throughout their lifespan.
13. Automotive
In the automotive industry, torque sensors are used for engine testing, measuring the torque output of the engine, and optimizing its performance. They are also used in transmission testing, measuring the torque transfer through the transmission system.
Automotive engineers rely on accurate torque measurements to fine-tune engine parameters, improve fuel efficiency, and reduce emissions. Torque sensors provide valuable data on the engine's performance under various operating conditions, allowing engineers to optimize the engine's power output and torque curve. This data is also used to calibrate the engine control unit (ECU), which manages the engine's fuel injection, ignition timing, and other critical functions.
Torque sensors are also used in the development and testing of electric vehicles (EVs). They are used to measure the torque output of the electric motor and to evaluate the performance of the drivetrain. Accurate torque measurements are essential for optimizing the efficiency and range of EVs.
In addition to engine and transmission testing, torque sensors are used in a variety of other automotive applications, such as measuring the torque applied to the steering wheel and pedals, and monitoring the torque in the driveshaft and axles. These measurements provide valuable insights into the vehicle's handling and performance, helping engineers to design safer and more enjoyable vehicles.
14. Aerospace
In the aerospace industry, torque sensors are used to ensure the safety and reliability of aircraft. They are used to measure the torque on critical components, such as bolts, fasteners, and control surfaces, ensuring that they are tightened to the correct specifications.
The consequences of a failure in the aerospace industry can be catastrophic, so precise torque measurement is absolutely essential. Torque sensors are used throughout the manufacturing and maintenance processes to ensure that all critical components are properly assembled and tightened. This includes everything from the engines and wings to the landing gear and control systems.
Torque sensors are also used in the testing of aircraft components and systems. For example, they are used to measure the torque on the control surfaces, such as the ailerons, elevators, and rudder, to ensure that they are operating within the specified limits. These tests help to identify any potential weaknesses or defects in the components before they are installed on an aircraft.
Furthermore, torque sensors are used in the monitoring of aircraft systems during flight. They can be used to measure the torque on the engines, propellers, and rotor systems, providing real-time data on the performance of these critical components. This data can be used to detect any potential problems early on, allowing pilots and maintenance personnel to take corrective action before a failure occurs.
15. Robotics
Robots rely on precise movements and control. Digital torque sensors are integrated into robotic joints and actuators to provide feedback on the force being applied. This allows robots to perform delicate tasks, like assembling electronic components or performing surgery, with incredible accuracy.
In robotics, torque sensors are often used in force/torque sensors, which are mounted on the robot's end-effector (the "hand" of the robot). These sensors provide information about the forces and torques that the robot is exerting on its environment, allowing the robot to adapt its movements and avoid damaging objects.
Torque sensors are also used in the development of collaborative robots, or "cobots," which are designed to work alongside humans. Cobots use torque sensors to detect collisions with humans and to automatically stop or slow down their movements to prevent injuries. This makes them safe and reliable for working in close proximity to humans.
Furthermore, torque sensors are used in the control of robot joints. By monitoring the torque on each joint, the robot can accurately control its position and orientation. This is particularly important for tasks that require high precision, such as welding, painting, and assembly.
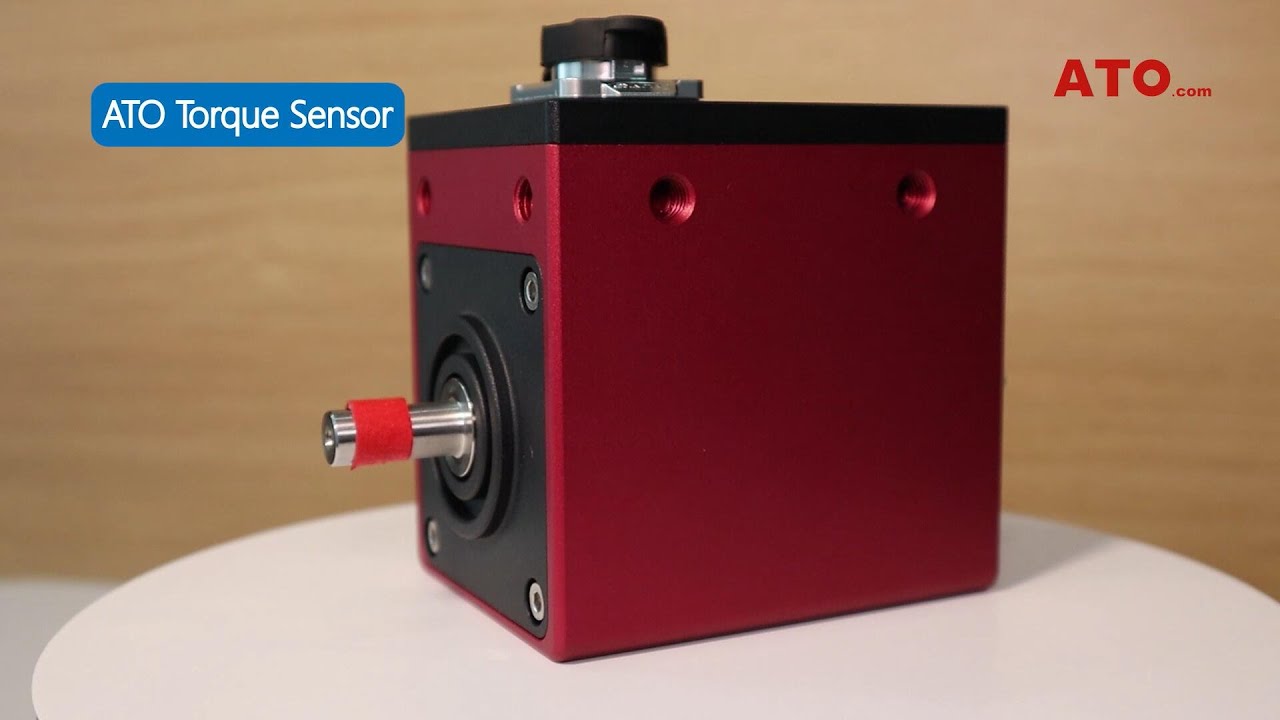
Digital Torque Sensor Wiring & Setting YouTube
FAQ About Digital Torque Sensors
16. Q
A: The primary difference lies in the output signal. Analog sensors produce a continuous voltage or current signal, while digital sensors output a discrete digital signal. Digital sensors generally offer higher accuracy, better noise immunity, and easier integration with digital systems.
17. Q
A: Calibration frequency depends on the application and usage. As a general rule, calibrate your sensor at least once a year. However, if the sensor is used frequently or in harsh environments, more frequent calibration may be necessary.
18. Q
A: Common sources of error include temperature variations, improper mounting, overloading the sensor, and electrical noise. Proper installation, environmental control, and regular calibration can minimize these errors.
