Nice Tips About How To Choose Busbar Size
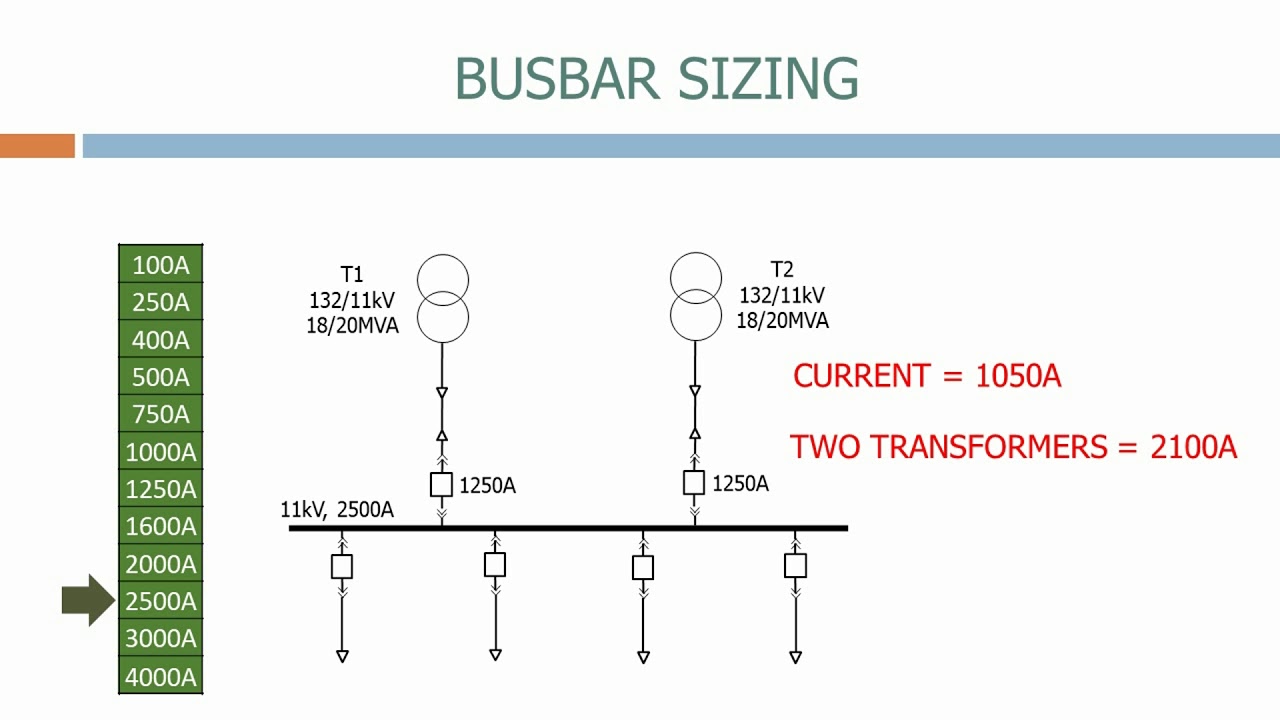
Understanding the Basics of Busbar Sizing
1. What is a Busbar Anyway?
Okay, so you're diving into the world of electrical systems and you've stumbled upon "busbars." Think of them as the power distribution hubs in your electrical setup. Theyre essentially metallic bars, usually copper or aluminum, that act like electrical highways, distributing current from incoming sources to multiple outgoing circuits. Without them, your electrical panel would be a tangled mess of wires! They're kind of a big deal, especially when considering how to choose busbar size.
Why is choosing the right size so critical? Well, imagine trying to force a river through a tiny pipe. Disaster, right? Similarly, an undersized busbar can overheat, leading to insulation breakdown, equipment failure, and, in worst-case scenarios, fires. On the flip side, an oversized busbar might be overkill — costing you more than necessary and taking up valuable space. So, getting it right is essential for safety, efficiency, and your wallet. Thats why understanding how to choose busbar size is more than just a technicality; it's about ensuring a robust and reliable electrical system.
Busbars come in various shapes and sizes, each designed for specific applications. You'll find them in switchboards, panel boards, and substations. They can be rectangular, round, or even custom-shaped, depending on the current-carrying requirements and the physical constraints of the installation. The material also plays a crucial role. Copper offers excellent conductivity but can be more expensive than aluminum. Aluminum is lighter and more cost-effective, but it may require larger dimensions to handle the same current. Selecting the appropriate material is definitely intertwined with learning how to choose busbar size effectively.
So, before we dive deep into the calculations and technical details, remember that the fundamental purpose of a busbar is to safely and efficiently distribute electrical power. The size of the busbar directly affects its ability to handle current without overheating. Understanding these basics sets the stage for making informed decisions when determining how to choose busbar size for your specific needs. Let's move on to the factors that influence this decision!

Busbar Sizing And Voltage Drop Calculation Excel Sheet
Factors Influencing Busbar Size
2. What to Consider Before You Measure
Alright, now that we know what a busbar is, lets talk about the things that dictate its size. Its not just pulling a number out of thin air! There are several key factors that come into play when figuring out how to choose busbar size, so buckle up.
First up: Current Capacity. This is the big one. How much current will the busbar need to handle? This isnt just a guess; it's a calculated figure based on the loads connected to the busbar. You need to consider both the continuous load (the steady-state current) and the peak load (the maximum current the busbar might experience). Don't forget to factor in any potential future expansion, because nobody wants to replace a busbar down the road just because they forgot to think ahead. Undersizing here will lead to overheating and potential failure, while oversizing will cost you unnecessary money. So, accuracy is key when estimating current requirements to help determine how to choose busbar size.
Next, we have Ambient Temperature. The surrounding temperature has a direct impact on the busbars ability to dissipate heat. Higher ambient temperatures reduce the busbar's current-carrying capacity. It's like running a marathon in the desert youre not going to perform as well as you would in cooler conditions. Electrical standards often provide derating factors for different ambient temperatures, so be sure to consult those guidelines. Ignoring this factor can lead to overheating, even if the busbar seems adequately sized for the current. It's a crucial consideration when deciding how to choose busbar size, especially in industrial settings or areas with extreme climates.
Another important factor is the Material. Copper and aluminum have different conductivity and thermal properties. Copper has higher conductivity, meaning it can carry more current for the same cross-sectional area compared to aluminum. However, aluminum is lighter and cheaper. So, the choice of material will influence the required size. Aluminum busbars, for instance, will generally need to be larger than copper busbars for the same current capacity. This directly affects the physical dimensions and overall cost of the busbar system. Don't just automatically go with the cheapest option; carefully evaluate the trade-offs between cost, performance, and space when learning how to choose busbar size.
Finally, Ventilation and Cooling. How well is the busbar ventilated? Is it enclosed in a cabinet, or is it exposed to open air? Good ventilation helps dissipate heat and increases the busbar's current-carrying capacity. Forced air cooling, such as fans, can further enhance cooling. If the busbar is enclosed with poor ventilation, youll need to derate its current capacity accordingly. This means selecting a larger size than you would otherwise need. Effective ventilation is often overlooked but can significantly impact the long-term reliability of the electrical system. So, make sure to consider the environment when determining how to choose busbar size.
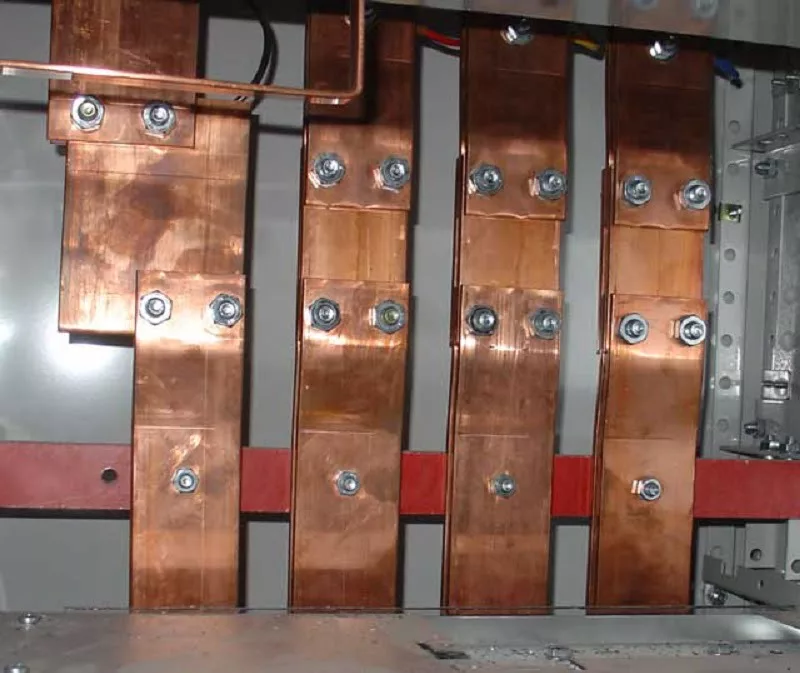
How Do You Design And Size A Busbar?
Calculating Busbar Size
3. Crunching the Numbers (Without Going Crazy)
Okay, so you've gathered all the information about current, temperature, material, and ventilation. Now it's time for the fun part: calculating the appropriate busbar size. Dont worry, well break it down into manageable steps. We aren't going to get too deep into the math, but a bit of calculation is essential to properly learn how to choose busbar size.
First, determine the Maximum Current: This is the highest current the busbar will likely experience. Include any safety factors or allowances for future growth. It's better to overestimate slightly than to underestimate, as undersizing can lead to serious problems. Use this maximum current as the basis for your calculations. Accurately determining the maximum current is the cornerstone of effectively choosing busbar size.
Next, find the Ampacity of the Conductor: Ampacity refers to the current-carrying capacity of a conductor. Look up the ampacity ratings for copper and aluminum busbars in relevant electrical codes and standards, such as the National Electrical Code (NEC) or IEC standards. These tables will provide ampacity values for different conductor sizes and materials, typically at a specific ambient temperature (e.g., 30C). This is a crucial step, so pay close attention to the tables and ensure you're using the correct values. Correctly finding ampacity is an essential part of learning how to choose busbar size.
Then, apply Derating Factors: Adjust the ampacity based on the ambient temperature and ventilation conditions. If the ambient temperature is higher than the temperature specified in the ampacity table, you'll need to derate the ampacity. Similarly, if the busbar is enclosed with poor ventilation, apply another derating factor. These derating factors are usually provided in the electrical codes and standards. Failing to account for these factors can lead to inaccurate sizing and potential overheating. Using the derating factors correctly help determine how to choose busbar size accurately.
Finally, Select the Appropriate Size: Compare the derated ampacity to the maximum current you calculated. Choose a busbar size that has a derated ampacity equal to or greater than the maximum current. It's generally a good idea to choose a size with a bit of extra capacity to provide a safety margin. Consider the mechanical strength of the busbar as well, especially for larger installations. Selecting a busbar that meets both electrical and mechanical requirements is crucial for long-term reliability. The final size selection is the culmination of all the previous steps in understanding how to choose busbar size.
Busbar Sizing ABB PDF
Practical Considerations and Best Practices
4. Tips for a Smooth Installation
Alright, you've crunched the numbers and chosen the right busbar size. But the job's not done yet! There are a few practical considerations and best practices to keep in mind during installation to ensure everything runs smoothly. Ignoring these can lead to problems down the line, even if the sizing is theoretically correct. So, lets take a look at the practicalities that need to be considered when learning how to choose busbar size for a specific application.
First off, Proper Support: Make sure the busbar is adequately supported to prevent sagging or bending. Sagging can stress the busbar and its connections, leading to reduced lifespan and potential failures. Use appropriate insulators and supports that are rated for the weight and operating temperature of the busbar. The spacing between supports should be in accordance with manufacturer recommendations or industry standards. Solid and properly installed supports are necessary when you learn how to choose busbar size.
Next, Secure Connections: Loose connections are a major cause of overheating and electrical failures. Ensure all connections are tight and properly torqued according to the manufacturer's specifications. Use the correct hardware and tools for the job. Periodically inspect the connections and tighten them as needed, especially in high-vibration environments. It's also a good practice to use a thermal imaging camera to detect hotspots that may indicate loose connections. Secure and tight connections are just as important when you learn how to choose busbar size.
Pay attention to Insulation and Clearance: Maintain proper insulation and clearance between the busbar and other conductive parts. This is essential to prevent short circuits and arcing. Use insulated busbar supports and barriers to ensure adequate separation. Check the clearances against relevant electrical codes and standards. Inadequate insulation and clearance can have serious consequences, including equipment damage and safety hazards. Insulation and clearance are factors that are vital to consider when learning how to choose busbar size correctly.
Dont forget about Labeling and Documentation: Clearly label the busbar and its connections, indicating the voltage, current rating, and circuit served. This makes it easier for future maintenance and troubleshooting. Keep accurate documentation of the busbar size, material, installation date, and any modifications made. This information will be invaluable for future reference. Properly labeled systems and thorough documentation are incredibly helpful when you learn how to choose busbar size for the long term.
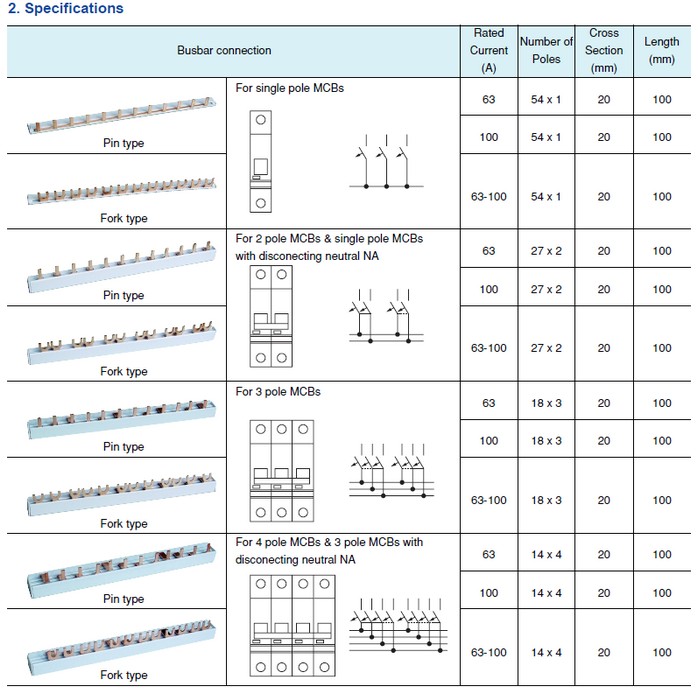
Troubleshooting Common Busbar Issues
5. What to Do When Things Go Wrong
Even with the best planning and installation, busbar systems can sometimes experience problems. Knowing how to troubleshoot common issues can save you time, money, and potential headaches. Let's delve into some common busbar challenges and how to address them. This knowledge is crucial for effectively applying what you learn about how to choose busbar size.
Overheating: This is perhaps the most frequent issue. Causes can include undersized busbars, loose connections, excessive load, poor ventilation, or high ambient temperatures. Use a thermal imaging camera to pinpoint the source of the heat. Tighten loose connections, reduce the load if possible, improve ventilation, or consider replacing the busbar with a larger size if it's undersized. Addressing overheating promptly is essential for preventing further damage and ensuring safety. Identifying the causes of overheating is important to fix the issue of learning how to choose busbar size.
Corrosion: Busbars exposed to moisture or corrosive environments can develop corrosion, which increases resistance and reduces current-carrying capacity. Clean corroded busbars with a suitable cleaner and protect them with a corrosion-resistant coating. Ensure proper ventilation to reduce moisture buildup. In severe cases, the busbar may need to be replaced. Prevention is better than cure, so consider using corrosion-resistant materials in the first place. Regular inspection and maintenance is key to prevent corrosion issues when you learn how to choose busbar size.
Arcing: Arcing is a dangerous phenomenon that can occur due to insulation breakdown, loose connections, or foreign objects coming into contact with the busbar. Immediately de-energize the system and inspect for any signs of damage. Repair or replace any damaged insulation or components. Ensure proper clearance and insulation to prevent future arcing events. Arcing can cause significant damage and pose a serious safety risk, so addressing it promptly is crucial. Fixing arc issue are very important after you learn how to choose busbar size.
Mechanical Damage: Busbars can be damaged by physical impact, vibration, or excessive stress. Inspect the busbar for any signs of bending, cracking, or deformation. Repair or replace any damaged sections. Ensure proper support and vibration isolation to prevent future mechanical damage. Mechanical damage can compromise the integrity of the busbar and lead to electrical failures. Preventing mechanical damage should also consider when you learn how to choose busbar size.
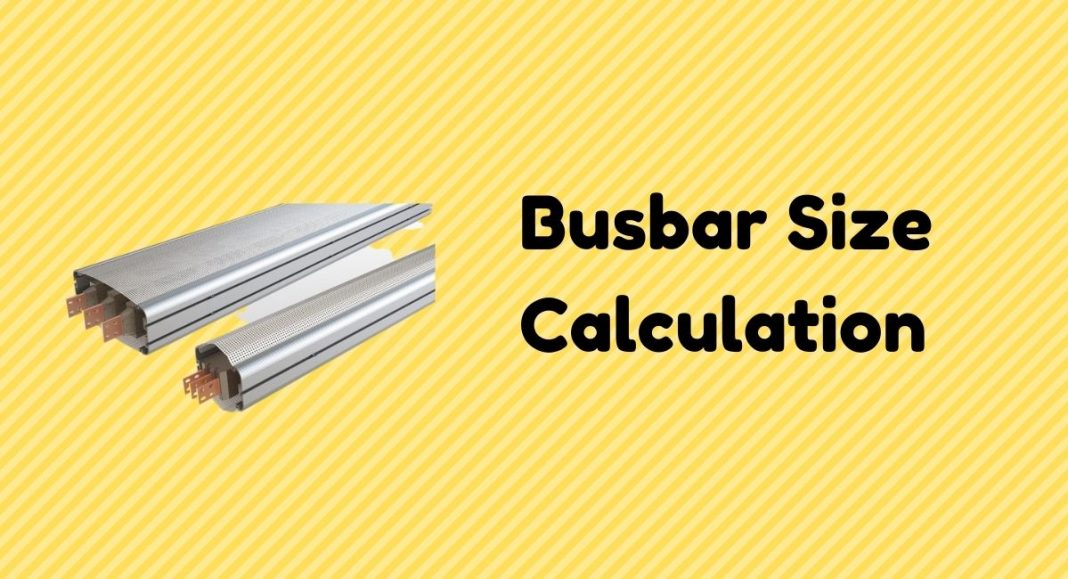
Electrical Panel Design Busbar Size Calculation Chart PDF Voltage Lab
Frequently Asked Questions (FAQs)
6. Your Busbar Questions Answered
Still have questions about choosing the right busbar size? Here are some frequently asked questions to help clarify things:
Q: What happens if I choose a busbar that's too small?A: An undersized busbar can overheat, leading to insulation breakdown, equipment failure, and potentially fires. It's a serious safety hazard and can result in costly downtime.
Q: Can I use aluminum instead of copper for busbars?A: Yes, aluminum can be used, but it has lower conductivity than copper. This means you'll need a larger aluminum busbar to carry the same amount of current as a copper busbar. Consider the trade-offs between cost, size, and performance.
Q: How often should I inspect my busbars?A: Regular inspections are crucial. The frequency depends on the environment and operating conditions. In general, inspect busbars at least annually, and more frequently in harsh environments.
Q: Where can I find the ampacity ratings for busbars?A: Ampacity ratings are typically found in electrical codes and standards, such as the National Electrical Code (NEC) in the US or IEC standards internationally. Consult these standards for specific ratings based on material, size, and temperature.